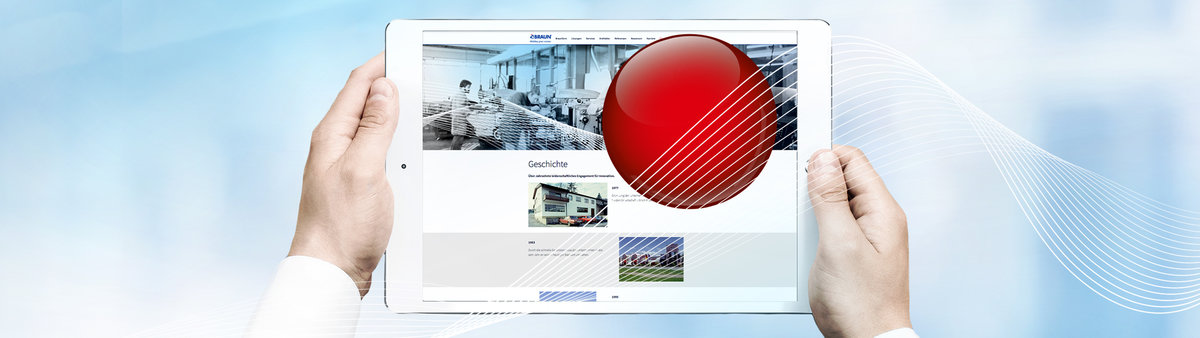
Higher efficiency due to simulations
– the classical mold maker evolves to Full Service Supplier.
20.07.2017
This year Braunform GmbH in Bahlingen and Endingen looks back to its 40-years success story. Due to the determination and the vision of the company in family ownership it becomes one of the leading manufacturers of injection molds and clean room products in Europe with more than 350 employees. The continuous development of the latest technologies, predictive investments in machinery and infrastructure as well as the enormous know-how of each individual are essential components of the company’s history.
The intention of the company is the steady advance of customer orientation as well as long-term success at the location Germany. Besides highest quality requirements for a mold maker, the economic conditions are often the determining factor for investments. A particular attention turns to the mold concept, the injection molding simulation and possibly occurring molding defects as well as their avoidance. Systematical quality planning and the potential for cycle time reduction are in focus to ensure sturdy processes and to improve the product performance.
The company can reach a higher efficiency by simulations. On the basis of a Moldflow® filling simulation it is possible to define optimal process conditions previous to the start of designing. As a standard, the existing article data is reviewed and analyzed in regard of mold-appropriate and production-oriented configuration. Optimization opportunities in terms of a sturdy mold design are developed based on pertinent experiences. Therefore it is essential to integrate the know-how obtained in mold shop and plastics processing with the idea of an industrialized production solution. The target is to offer a complete package of possibilities to the customer, increasing the production efficiency and ensuring maximum quality of the final product – the plastic part.
The article design is developed by Braunform in cooperation with the customer and professional partners. As a standard, a simulation is carried out in the design phase of each mold with the aim to integrate the perceptions in the mold design. Initially it contains an ordinary and statistical plastic filling simulation in order to predict the behavior of the thermoplastic materials during injection process. This offers the opportunity to recognize injection failures e. g. weld lines, entrapped air and sink marks in advance. The risk of injection failures is minimized and there arise possibilities to act accordingly. Braunform takes the results out of the simulation as a support to deviate optimization arrangements i. a. for the quality and process safety. The customer receives a significant documentation according to prior agreement.
In recent years the company has particularly invested in new technologies such as the expansion of competences in the area of DFM (design for manufacturing). DFM refers to a concept during the product development process, in which a production-oriented configuration or adjustment of article design is already considered in the development itself. By means of consistent DFM, quality-, performance- and availability losses can be avoided in the subsequent serial production. As a foresighted quality planning, a DFM aims to increase production efficiency. Injection molding simulation is an essential tool for this.
Braunform integrates itself into the development process at an early stage with visionary, innovative mold solutions. Together with our customers, production processes will be investigated with the intention to optimize article design, improve quality and produce more steady and economical.
In order to ensure an optimal cycle time, the optimal injection position is determined, the hot runner system is integrated and the efficiency of the cooling system is considered. Furthermore the part and mold design is checked regarding shrinkage and deformation. Accuracy and obligation is based on a statistical approach.
Basis for an exact prediction of the injection process is the possibility to consider each detail of the mold in the simulation. Starting with simple calculations of a component part, followed by verification of tempering concepts, the system can easily be extended to DOE optimizations in “Virtual Molding” principle. Based on the presentation of real thermal and rheological processes of the mold system, the simulation provides a reliable basis for decisions in the development process.
By means of Quality Engineering, the company goes beyond traditional mold making in order to be responsive to the present customer requirements. This approach follows three perspectives: technical, functional and Quality Assurance (QA) expertise. The technical expertise applies to the product closeness; functional expertise considers the customer closeness and the QA expertise serves the systematic quality planning and risk management. Quality characteristics like availability, reliability and performance are essential issues. In this complex proximity, quality goals will be reached by a cooperative process. Achieving the quality goals is a central component of this process.
Contact Person
Marketing
Tel. +49 (0) 7663-9320-0
marketing@braunform.com