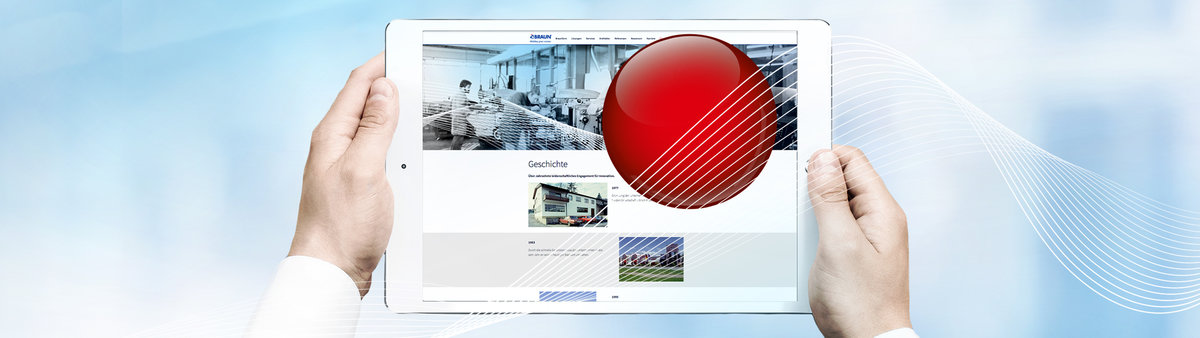
FAKUMA 2015
Braunform established four patented innovations in the field of index molds and expands its services.
30.08.2015
Due to the objective to offer the end user superior products, the demand for functional molds of the highest quality is increasing. The product function is not only decisive for the design and haptic but also for the related mold concept. An optimal implementation of these requirements may, for example, be achieved by the use of the multi-component technology. Using this it is also possible to map complex geometries, to combine different materials and to connect all this to an attractive design. On the one hand, it is the upgrading of the product in regard to visual criteria, design and haptic. On the other hand the multi component technique influences tremendously the function of the product (for examples tamper evident and sealing functions) and it saves cost intensive assembly steps at the plant of the producer.
Since building the first 2-component injection mold in 1986 Braunform invested in multi-component technology and steadily expanded its technological expertise. Today, the technology portfolio includes rotary table molds and injection molds with integrated turntable, core-back molds, injection molds with an internal or external mold handling. Also stack turning techniques such as Gram-technology as well as the cube technology are used frequently. To achieve the highest geometric freedoms especially the index mold technology is the best choice. However, which method is used is ultimately determined by the article itself and the required quantities.
Using the firmly established company philosophy to protect intellectual property, four innovative solutions have been brought to patent in the field of index molds.
For the secure injection molding of plastic articles normally a stripper ledge is used to release the inside part of the article from the core. Here, however, small wiping surfaces in the conventional type of mold can cause high demolding forces and thus damage the product.
With the solution of Braunform to move the plastic part by means of mold inserts to the mold core a safe demolding is guaranteed. With the stripper a distribution of stripping forces on several sides of the plastic part is carried out. Thus, a deformation of the plastic part is prevented.
By integrating the ejector in the index a new solution for a more compact design is created. The "Index Ejector” is beneficial for long hollow cylindrical moldings. The ejector configuration can take place perpendicular to the opening direction. This effects new visual representation of geometric degrees of freedom which did not exist until now.
By means of the “Index Stripper System” solution an easier actuation of the stripper ledge and a reduction of the cycle time is possible. This is achieved by a linear guided stripper ledge. This moves the stripper ledge synchronously to axial movement Index. Before, the mold opened and the stripper ledge was actuated by a separate drive. Now this drive is eliminated and two operations are merged into one. Moreover, it is possible to manufacture a product having no ejector marks on the outer surface.
In classical multicomponent applications which are produced by means of index molds, the design of the individual molding components depends on the others. The reason for this is the limitation that, for example, breakthroughs or injection points must be oriented effectively in mold or slider opening direction. But shall now, for example, the injection points of various components be arranged regardless of their radial position to each other this is possible by an additional rotation of the index core. The "Index Turning Technology" creates new design possibilities for multi-component parts as the degrees of freedom are substantially increased. This new type of index-tools can be used both for the production of hollow cylindrical, and for the full-body-like molded parts.
Not only innovative, technical solutions are top priority at Braunform but also the customer needs in the field of service:
With the innovative mold-shop and a deep understanding of technology as a starting point, it is also the value-added services related to the mold that represents the difference for customers of Braunform.
These additional services are included as standard in the quotation or offered to customers as extra options. The goal is to make the service package more transparent for the partners. The customer should exactly know what he receives for his investment. What kind of performance they can expect from Braunform as standard without additional costs and what other additional options he can order. Input from many discussions with customers has been taken to develop these targeted services.
It is standard to analyze existing article data during design phase in regard to a design that considers the needs of the mold and production. Beside a further risk minimization by Mold-Flow filling simulation, optimal industrialized manufacturing solutions can be guaranteed. The complete documentation (incl. CE marking) and a lettering of the mold parts is included in the standard.
In addition to analyzing the articles in regard to the needs of the mold and production, optimization possibilities were specifically developed to improve product design for subsequent series production. Here the expertise of toolmaking and plastics processing needs to be integrated with the idea of an industrialized manufacturing solution. The article data are subject to change based on a joint agreement and demarcation of responsibilities. Upon completion and approval of the revised data, the customer receives a documentation of the changes.
In the Braunform technology center the ideal injection molding process is determined based on statistical methods and experiments step by step. Using software solutions from AST ideal parameter sets for the melting treatment, the injection and holding pressure behavior are analyzed systematically.
Based on the product drawing initial sample inspection reports (ISIR) are created. Therein amongst others the testing methodology will be noted, the documentation will be adapted, the article drawing is marked, measuring programs are created and parts are measured. Together with the ISIR the number of the measured critical dimensions is determined together with the customer. Over a defined period samples are taken, the agreed dimensions are measured and the cpk value is determined.
A CT measurement can cover further services, such as target/actual comparison between the CAD model and the 3D model of the reconstructed CT data, the conversion of a 3D model in a 3D CAD model as well as a defect and failure analysis.
In cooperation with the customer measuring devices are designed and built for the later measurement.
The aim is to offer customers a product that increases the effectiveness of his production and ensures that the end product - the plastic part - meets the quality requirements. As owners of the company, Erich and Pamela Braun are dedicated to this goal. Especially in Europe this holistic quality is inevitable.2015_FAKUMA_1.pdf
Contact Person
Marketing
Tel. +49 (0) 7663-9320-0
marketing@braunform.com