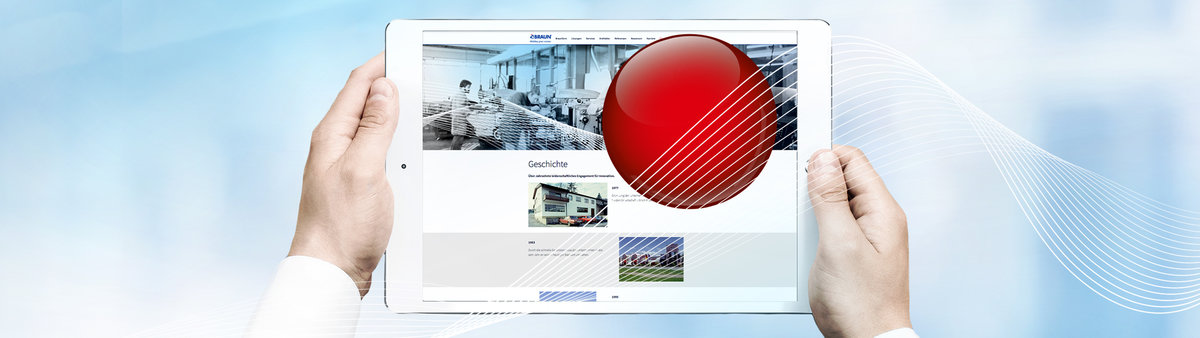
Injection molds with quick-changing system
Maximum efficiency and flexibility
09.09.2014
In addition to the highest quality standards in a today’s mold-shop it is the economic aspect that often proving decisive for an investment. Multi-cavity injection molds with high output rates must come up with a short cycle time with great flexibility and ease of maintenance. Also evident in the consideration of social trends is the increasing consumer demand for individual products or different product variants across industries.
This results in a correspondingly large number of mold variants often characterized by locally differently shaped geometries. For this, in turn, different mold cores or mold pins are required which have to be replaced in the normal process by costly assembly work. Therefore, for the manufacturing of various mold variants, the interchangeability of mold cores and pins is a flexible, inexpensive alternative without long set-up times.
The patented Braunform systems are distinguished by the quick-change system of individual areas and the modular design.Through simple operation of a locking device cores and pins of different geometries are exchangeable within the quick-change system while in the modular design complete components and thus large-scale forming areas can be replaced by simple handgrips. Here, a solution for replacing nozzle side inserts was created in which a side gate nozzle is implemented. The module designed can be separated from the mold during disassembly by a releasable electrical connection at the mold without additional work, so complex wiring work is eliminated.
The modular design allows more compact injection molds, whereas each module is almost like a small tool. Due to the direct centering of the inserts ejector side to nozzle side wear is minimized, since with floating cavities the thermal expansion of the mold plates has a minor influence. The modules can be used in a pilot mold for testing purposes before the final installation takes place in the production mold. Thus, the pilot phase brings both a risk minimization as well as a project safety resulting in a time advantage in the optimization phase.
Thanks to this cost efficiency i. e. by reduced set-up times, higher costs for the pilot and production mold amortize within a very short time. In cases of maintenance or repair the modules can be replaced quickly so there is hardly any loss of production and production can start again very fast. Another advantage shows in pharmaceutical applications and plastics production in the clean room. As during set-up only one module needs to be replaced by quick-change system the time consuming in- and outward transfer of the complete mold into the clean room is eliminated.
Contact Person
Marketing
Tel. +49 (0) 7663-9320-0
marketing@braunform.com