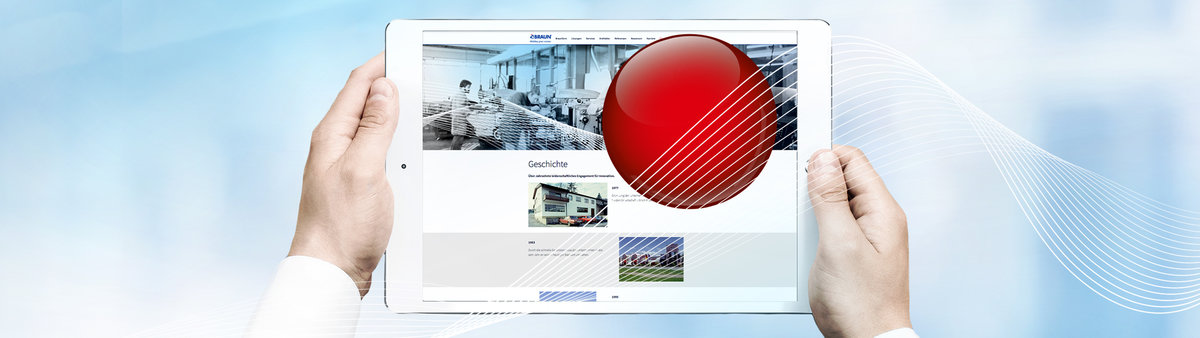
Höhere Produktivität dank Simulationen
– der klassische Formenbau entwickelt sich zum Full-Service Dienstleister
20.07.2017
Dieses Jahr blickt die Braunform GmbH in Bahlingen und Endingen am Kaiserstuhl auf ihre 40-jährige Erfolgsgeschichte zurück. Der Zielstrebigkeit und dem Weitblick des Unternehmens in Familienbesitz ist es zu verdanken, dass es heute mit über 350 Mitarbeitern zu den führenden Herstellern von Spritzgießformen und Reinraumprodukten in Europa zählt. Die stetige Weiterentwicklung neuster Technologien, vorausschauende Investitionen in den Maschinenpark und die Infrastruktur sowie das enorme Know-How jedes Einzelnen sind essentielle Bestandteile der Unternehmensgeschichte.
Das Ziel des Unternehmens ist das stetige Voranbringen der Kundenorientierung sowie der langfristige Erfolg am Standort Deutschland. Neben höchsten Qualitätsanforderungen an einen Formenbau, sind es die wirtschaftlichen Randbedingungen, die häufig den Ausschlag für eine Investition geben. Ein besonderes Augenmerk richtet sich auf das Werkzeugkonzept, die Spritzgießsimulation und eventuell entstehende Formteilfehler und deren Vermeidung. Die systematische Qualitätsplanung und das Potential für Zykluszeitverkürzungen stehen im Vordergrund, um robuste Prozesse und somit die Produkteffizienz zu verbessern.
Das Unternehmen kann eine höhere Produktivität durch Simulationen erreichen. Anhand der Moldflow® Füllsimulation können so optimale Prozessbedingungen schon vor Beginn der Konstruktion gewählt werden. Vorhandene Artikeldaten werden standardmäßig hinsichtlich werkzeuggerechter- und fertigungstechnischer Gestaltung untersucht und analysiert. Basierend auf einschlägigen Erfahrungen werden Optimierungsmöglichkeiten im Hinblick auf eine robuste Werkzeugkonstruktion erarbeitet. Essentiell ist hierbei das Integrieren von Know-how aus Werkzeugbau und Kunststoffverarbeitung mit dem Gedanken an eine industrialisierte Fertigungslösung. Ziel ist es, dem Kunden ein Gesamtprodukt anzubieten, das die Effektivität seiner Produktion erhöht und das maximale Qualität für das Endprodukt – das Kunststoffteil – gewährleistet.
In Zusammenarbeit mit dem Kunden und professionellen Partnern entwickelt Braunform das Artikeldesign. Bei jedem Werkzeug wird bereits in der Designphase standardmäßig eine Simulation, deren Erkenntnisse direkt in die Werkzeugkonstruktion einfließen, durchgeführt. Es handelt sich dabei zunächst um eine einfache und statistische Kunststoff-Füllsimulation, mit deren Hilfe das Verhalten der thermoplastischen Kunststoffe während des Einspritzvorgangs vorhergesagt werden kann. So werden Spritzgießfehler wie z. B. Bindenähte, Lufteinschlüsse und Einfallstellen, vorab erkannt. Das Risiko von Spritzfehlern wird minimiert und es entstehen Möglichkeiten, entsprechend zu agieren. Braunform interpretiert die Ergebnisse aus der Simulation, um daraus Optimierungsmaßnahmen u. a. für die Qualität und Prozesssicherheit abzuleiten. Der Kunde erhält nach der gemeinsamen Vereinbarung eine aussagekräftige Dokumentation.
In den letzten Jahren wurde insbesondere in neue Technologien investiert, wie z. B. in die Ausweitung der Kompetenzen im Bereich DFM (design for manufacturing). DFM bezeichnet ein Konzept während der Produktentwicklung, bei dem bereits in der Entwicklung selbst auf eine produktionsgerechte Auslegung bzw. Anpassung des Artikeldesigns geachtet wird. Durch konsequentes DFM sollen Qualitäts-, Leistungs- und Verfügbarkeitsverluste in der späteren Serienproduktion vermieden werden. Die DFM zielt als vorausschauende Qualitätsplanung darauf ab, die Produktionseffizienz zu steigern. Die Spritzgießsimulation ist hierfür ein essentielles Werkzeug.
Als Ideenlieferant bringt sich Braunform mit visionären, innovativen Formenbau-Lösungen schon frühzeitig in den Entwicklungsprozess mit ein. Gemeinsam mit unseren Kunden werden deren Produktionsabläufe durchleuchtet mit dem Hintergrund, das Artikeldesign zu optimieren, die Qualität zu verbessern und um stabiler und wirtschaftlicher zu produzieren.
Um eine optimale Zykluszeit zu gewährleisten, wird die optimale Anspritzposition ermittelt, das Heißkanalsystem integriert sowie die Effizienz des Kühlsystems betrachtet. Ebenso wird die Teile- und Werkzeugkonstruktion auf Schwindung und Verzug überprüft. Die Genauigkeit und Verbindlichkeit entspricht einer statischen Betrachtungsweise.
Die Möglichkeit, alle Details des Werkzeuges in der Simulation zu berücksichtigen, ist die Basis für die genaue Vorhersage des Spritzgießprozesses. Beginnend mit einfachen Berechnungen eines Bauteils, gefolgt von der Prüfung von Temperierkonzepten, kann das System bis hin zu DOE Optimierungen im „Virtual Molding“ Ansatz einfach erweitert werden. Basierend auf der Abbildung realer thermischer und rheologischer Prozesse des Werkzeugsystems liefert die Simulation eine verlässliche Basis für Entscheidungen im Entwicklungsprozess.
Mittels Quality Engineering geht das Unternehmen über den traditionellen Werkzeugbau hinaus, hin zu den heutigen Kundenbedürfnissen. Dieser Ansatz folgt drei Blickwinkeln: die technische, die funktionelle und die Quality Assurance (QA) Expertise. Die technische Expertise bezieht sich auf die Produktnähe, mit der funktionellen Expertise wird die Kundennähe berücksichtigt und die QA Expertise dient der systematischen Qualitätsplanung und dem Risikomanagement. Qualitätsmerkmale wie Verfügbarkeit, Zuverlässigkeit und Performance sind essentielle Aspekte. In dieser komplexen Umgebung werden Qualitätsziele durch einen kooperativen Prozess umgesetzt. Die Erreichung der Qualitätsziele ist zentraler Bestandteil dieses Prozesses.
Ansprechpartner
Marketing
Tel. +49 (0) 7663-9320-0
marketing@braunform.com